|
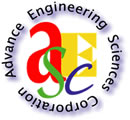 |
|
Delivering Advanced Engineering Solutions |
|
|
|
|
|
AESC considers FMECA as an effective tool for evaluation of clients system throughout design, pre and post production phases. During the design phase recommendations and weakness identification has proved an invaluable cost savings mechanism that our clients have counted on in all their projects. Utilization of FMECA for pre and post production phase has also proved to be very effective in identification of safety risks that have helped avoid risk to operators, and public.
Failure Mode and Effects Analysis (FMEA), and Failure Mode and Effects Criticality Analysis (FMECA), are processes by which potential weaknesses in design or a process is identified. FMECA as described in MIL-STD-1629A, and FMEA as described in ISO9000, involve reviewing schematics, engineering drawings, operational manuals, etc, to identify basic faults at the lowest (part) level and consequently determine their effects at subassembly (higher) level, or system level with respect to safety and or operational requirements. This approach is also considered as an inductive analysis that methodically details, on an element-by-element basis, all possible failure modes and identifies their resulting effects on surrounding elements and or the overall system.
If identified weaknesses or risks, cannot be corrected by way of redesign we develop fault tree, and event tree models to assess the potential risk and consequences. There are scenarios where a redesign is either not feasible or not possible, in which case we can try to mitigate risk. We also apply FMECA in combination with fault tree analysis as part of our root cause analysis solution.
|
|
|
|
|
|